Sophie Preece
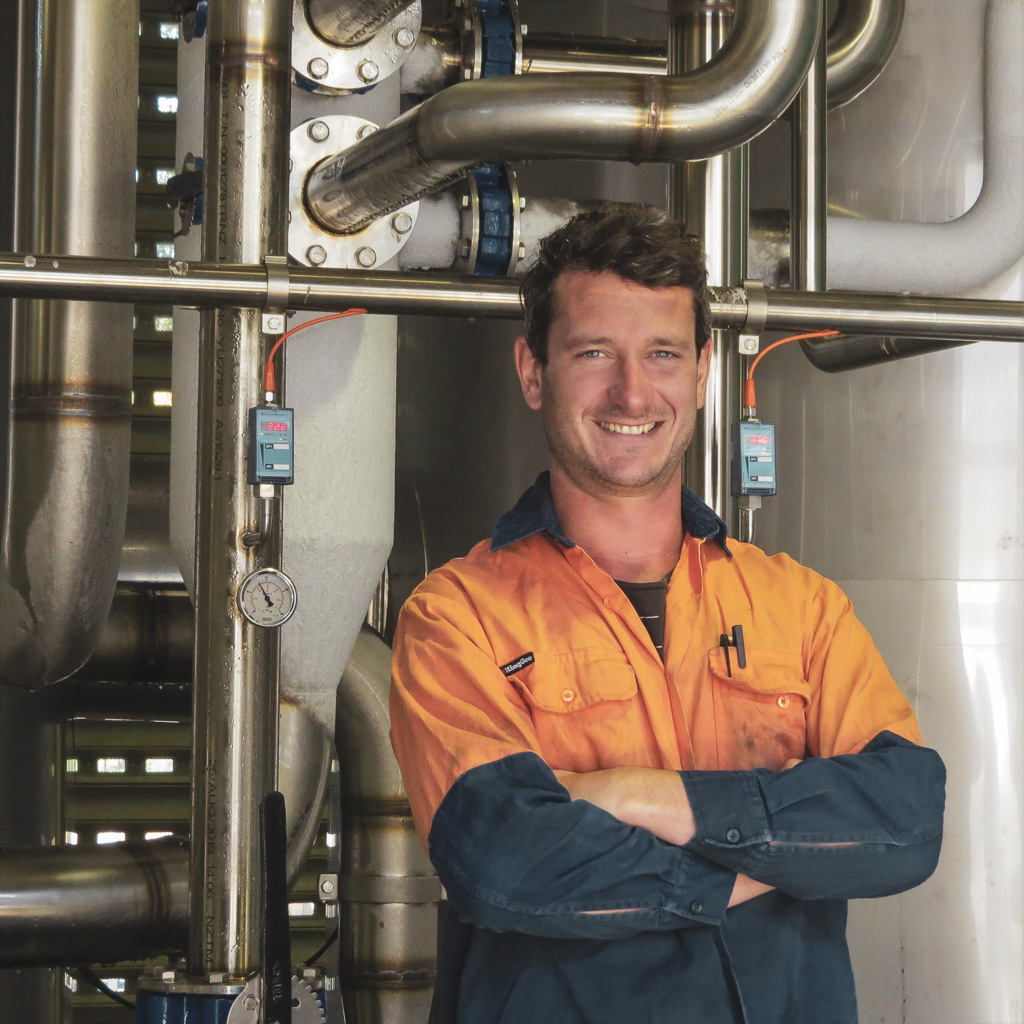
The founder of Ash Engineering Ltd, a specialist in stainless steel tube fitting in Marlborough wineries, is a walking, talking advertisement for apprenticeships.
“Trades deserve more respect out there and I really rate it as a professional choice,” Ash says from Cloudy Bay winery, one of his favourite places to work. “This place is wicked – they want all the work to be at the highest level and I love that. I want it to be to that level too.”
His excellence in the trade, in a region that’s reliant on farms of gleaming steel, is a far cry from his experience at secondary school in Dunedin. He had just started his 6th form year when he decided he was being “brainwashed” into thinking university was the only way forward. “I was hopeless, so I ended up leaving. It just didn’t suit me and I knew I wanted to do something tangible.”
Ash grew up on a sheep and beef farm in West Otago and from a young age could be found in the shed making things, including go-karts with his father. “I just loved it. I was always in there welding things…I loved the end result. The satisfaction. And learning along the way.”
After leaving school he spent six months doing a pre-trade course in mechanical engineering, followed by two years in a meatworks doing maintenance engineering and diagnostics. It paid $8.60 an hour to begin with, and Ash had to seek a top-up from his parents to get through. “It proves you have to be patient,” he says. “You just have to have some vision.”
When he left the meatworks, Ash finished his apprenticeship and set up Ash Engineering. Then he went on the road for four years, “living out of a suitcase, building those big (dairy) factories you see in the middle of nowhere”, and learning all the stainless steel pipe fitting and installation skills he needed.
Then two years ago he came to Marlborough, where his parents had purchased vineyards and the wine industry was in a constant expansion phase. After six months of sub-contracting, Ash caught the eye of what would become clients and was able to source business on his own.
He stands in a room of his work, where tubes of stainless snake up walls, bending and linking here and there to ensure a seamless, gleaming connection of pipes; all designed, created and installed by Ash. “This one was all made on the spot – there were no plans. I just thought, how will we make it work, make it fit?” It’s the same way he has worked since making those go-karts as a kid, or the big motocross ramp he made in his teens. “I can visualise it really well. How it needs to be.”
These days Ash runs a workshop in one of his parents’ unused vineyard sheds, moving between there and onsite jobs. And despite the success and growth of his business, he’s still as excited as a kid with a go-kart - working with a welder, music playing in the background, to transform steel into a vital component of a factory.
If he’d known this would be the outcome when he left school, it would have been easier to smile through all the “frowning” of others, he says. “I didn’t think this far ahead. I just saw engineers who were good and knew I wanted to be like them.”
This story was first published in Winepress Magazine and is reproduced with their permission.